Stucco and the blind man
Chapter 6 - Plaster: interior plaster
Updated February 06, 2023
Stucco is a name for cement plaster, that is cement or lime (or other material) mortar applied mainly to the outside of a building, and in many cases to the inside of the building.
There seems to be little known these days about interior plaster. Interior plaster is also known as gypsum plaster, but lime plaster and mud plaster (clay soil and sand) and other materials for wall construction have been used over the years that have no gypsum at all. Plaster in this case refers to mortar applied to the wall, gypsum plaster or other materials.
The verb plaster means to apply mortar to a wall or ceiling but not necessarily gypsum plaster. Plaster as we know it today comes in a bag that says the word "plaster" on the bag. Plaster is not ez sand, drywall compound, or handy patch material from the home supply. Another thing plaster is not is a material applied to a wall and then sanded down. We were patching and old church and someone asked me if that was EZ sand. I told him it was hard sand, or better yet impossible to sand. EZ sand is a soft weak material which is why it can be sanded.
I wanted to add a couple things that are important. One thing that plaster is not is drywall materials. Sadly enough frequently plaster is repaired with drywall materials. A hole in a ceiling may be filled with a piece of sheetrock with tape and mud gobbed around the edges. This might be fine in normal lighting, however when the sunlight hits the wall or a bright light hits the wall it looks like a relief map of a mountain range. It reminds me of the relief globes that we had in school with raised mountains and lowered valleys. Using real plaster allows the patch to be straightened and filled to the level of the old ceiling and allows the edges of the patch to join flush to the edges. The patch should be invisible. or it worst inconspicuous. Plus, using a durable material improves the overall quality of the ceiling.
Another thing plaster is not, is marmarino. Marmorino is used for color venetian plaster finishes. Marmarino is a material that is like drywall mud and doesn't set hard like plaster. We did a Pottery Barn store and two Williams-Sonoma stores with marmarino years ago, about 1996. I decided then, that I would only want to work with real plaster. Adding color to the plaster has better color effects and it's a far better quality material. Marmarino can be scratched easily with your fingernail. Real plaster with color in it has elegant effects and even if plaster is applied thin, there is a solid knock on the wall quality and you can't beat the smooth, stone like finish.
Plaster is the same material used for casting, which was real popular in the 1950's and before, when plastic products weren't widely available. All plaster, that is gypsum plaster, is a form of plaster of paris. The brown or greyish plaster is made to be mixed with sand or light weight aggregate for plaster basecoats, where the white plaster, molding plaster or gauging plaster are made to be mixed with lime for finish coat plaster. Pure molding plaster is be used for casting or for running moldings on a bench. Run in place moldings are made using lime in the mortar. The lime adds workability allowing the mechanic to apply and work with the mortar. Bench run moldings use pure molding plaster because applying the mortar doesn't have to defy the force of gravity.
We are fortunate to live in the information age, but we also live in the misinformation age, so misinformation about plaster and plastering in general spreads in milliseconds and globally. My mission is to sort out the truth based on experience and provide information based on experience and not hearsay.
The main types of interior gypsum plaster used today are conventional plaster and veneer plaster. I covered lime and sand basecoats with hair on wood lath back in Mortar and sand.
When I say conventional plaster I mean a thick base coat of 1/2" to 3/4" or more applied over block or lath, either gypsum lath (rock lath ) or metal lath. For years I worked on high abuse walls for hospitals, schools, government building corridors, etc. applying plaster to block walls. Dollar for dollar, there is no more durable and practical material for high abuse walls than conventional plaster. The plaster used was gypsum plaster and sand, the ratio normally was 20 shovelfuls of sand to 1 100 lb. bag of plaster. Gypsum plaster can also be mixed with lightweight aggregate and not sand, but sand mortar is a lot stronger and can't be used for government type work such as high abuse walls. State of Virginia work and even federal government work prohibited the use of lightweight aggregate. The basecoat plaster sold in Home Depot and other home stores is gypsum plaster premixed with perlite, a lightweight aggregate. This is convenient and easy to use for a handy andy or harry homeowner, but is too weak to be used in hospital corridors and simply doesn't have the quality of sand mortar.
There are some advantages to lightweight aggregates, such as light weight and better fireproofing qualities. The two types of light weight aggregates are perlite and vermiculite. You may recognize the names from the garden supply. Vermiculite is used in gardening because it absorbs water and retains water around the roots of the plant. The difference between vermiculite and perlite is that vermiculite has larger coarser grains than perlite. Perlite has small round particles. Years ago, we used a brand of vermiculite called Zonolite, which had dark color grains. Perlite and vermiculite are made from mica, the rock. The dust or fine particles of mica are heated until they expand like popcorn. Speaking of popcorn, vermiculite is used in acoustic spray ceilings, also known as popcorn ceilings. Popcorn ceilings are a mixture of vermiculite and drywall mud. Vericulite and perlite are also used in paint for a sand finish or a fake stucco look like in Reston, Virginia.
Lightweight aggregates should NEVER, EVER, EVER be used on metal lath. Only sand mortar should be used for metal lath walls and ceilings. For years it said on the bag of strucro-lite, US Gypsum's brand of pre-mixed perlite plaster "Not recommended for use on metal lath". Why they took the warning off the bags, I don't know, except that it is difficult to find unmixed gypsum plaster these days. We called unmixed gypsum plaster "hardwall", which is Gold Bond brand's name for unmixed gypsum plaster. Basecoat plaster is usually called brown mortar, with sand basecoats called sand mortar. Sometimes hardwall was called Red Top plaster after USG's brand for plaster products. This is what it means when you hear these terms.
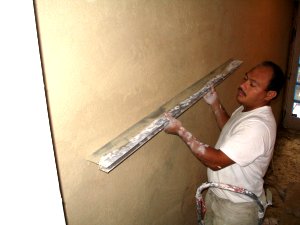
Rodding off plaster brown coat.
What is "Neat" plaster ? Neat plaster is brown mortar with no sand or aggregate. That is unmixed gypsum basecoat plaster with no sand. For example, instructions may say mix 100 lb.s neat plaster with 4 cubic feet of sand. About 30 years ago, we took over a job from an EIFS contractor who was completely inexperience and unqualified to do this work. The government specified wood fibered plaster which is high strength basecoat plaster that was special ordered for the job, for a building that had a lot of abuse. The instructions on the bag said "plaster to applied neat. For high suction surfaces such as block up to 9 shovels of sand may be added for each bag." These people added 16 shovels of sand per bag, and on top of that retempered the mortar. If you read my chapter about mortar and sand, you'll see plaster should never be retempered. This mortar was knocked off the wall easily. We knocked off the brown coat leaving the scratch coat on metal lath. There simply wasn't time or money to tear off everything and start over. The result was an inferior product. Instead of a very high abuse wall surface, the government had the opposite. Believe it or not, this person is advertises in the Blue Book and other places as a plastering contractor. When is a plastering contractor not a plastering contractor ? These EIFS and drywall contractors have no business bidding on plaster jobs. One really needs to be careful in who they hire. This is a sad comment on the bid system which should be overhauled. What was once an opportunity for the little guy has provided a free for all for the unqualified contractor. Some people are so incompetent they believe they are competent. The Dunning Kruger effect.
Check out this Youtube video, The Dunning Kruger song, from the incompetence opera
I am going to cover finish coat plaster. or white mortar before I jump to veneer plaster.
The best explanation of finish mortar is my youtube video here:
Making a gauge-mixing gauging plaster and lime on the mortar board.
Mixing finish plaster on a mortar board is called making a gauge, which is where the name gauging plaster comes from. Lime is mixed with water by various methods and put on the mortar board. This is called lime putty. Here we call the finish coat of plaster white coat, and in California the finish coat of plaster is called a putty coat. The lime on the board is formed into a ring, then water poured into the ring. Then the gauging plaster is sifted into the water. You gotta see the video. The ratio of lime to plaster is between 3:1 to 1:1. 1:1 is the strongest and 3:1 is the weakest. Pouring the water into the ring determines the ratio of lime to gauging. This is called setting the gauge. I worked for companies where the oldest plasterer set the gauge.
Molding plaster can be used instead of gauging plaster. I prefer molding plaster over gauging most of the time. The only difference between molding plaster and gauging plaster is that molding plaster has a finer grain. Molding plaster is made for moldings and casting. It gets really super hard and is great for patch work. Gauging plaster with it's coarser grain sinks into the water faster for making a gauge faster. We always called finish plaster, that is lime and gauging (or molding) white mortar. White mortar is great for patching because it sets fast and is really hard allowing even deep patches to be done the same day, or usually within the same hour.
As a warning, this white mortar is great for metal lath and block, it should never be used over rock lath or blue board (veneer plaster base) with out a basecoat. White mortar will peel off easily and the joints will crack. They make a finish coat material for applying directly to blue board. One trick I learned is to mix in some white silica sand in the white mortar for patching over rock lath, but there isn't any need to.
Veneer plaster, sometimes called one coat or thin coat plaster, is an excellent alternative to drywall. The surface is hard and chip resistent but you can still kick a hole in the wall. Water resistent finishes can be used like Keene's cement for scrubbable bathrooms and kitchen. I'll laugh when you scrub your level 5 drywall off the wall. There are two systems for veneer plaster, the one coat system and the two coat system.
You may want to check out what I wrote about veneer plaster by clicking on this link. For pics of some of our veneer jobs, please check out my plaster gallery by clicking here.
The veneer plaster base, or blue board, is sheetrock color coded blue, or greyish blue. This is never to be confused with mold resistent board or green board for bathrooms. The only difference between blue board and conventional wallboard is the face paper is a little more porous for a good bond.
Thin coat plaster is excellent for resurfacing old walls and ceilings that are in stable condition, even if the paint is peeling some and there is some damage. The old walls need to be painted with plaster weld or a quality bonding agent.
Veneer basecoat plaster is super hard even though it is applied thin. Sometimes, it makes sparks when you scrape it. Veneer basecoat is made with hardwall, fine silica sand and accelerator. This mortar sets real fast, allowing this basecoat to be put on thin without dry-outs. That is it sets before it dries.
Using veneer basecoat allows use of various finishes. We generally just use our lime and gauging plaster over the basecoat and it works fine. Also Red top finish plaster (USG) or Kal-Kote (National Gypsum) can be used. These finish plasters can be mixed with a drill in a large container or buckets for speed in mixing. These are gauged light, that is, 3:1 lime to gauging and aren't as hard and scratch resistent as heavy gauged (1:1) lime and gauging.
There are finish plasters made for one coat application, without the veneer basecoat. Two coats, however are better than one. USG makes Diamond Finish and also Norfolk Veneer for one coat application on veneer board. Diamond finish can be mixed with a drill and put on blueboard with one coat. I have found this material too difficult to work with so we don't use it. Norfolk veneer is used widely in the Tidewater area of Virginia where veneer plaster is still popular. I think it is made in Norfolk. We used it before in Arlington, Virginia.A plasterer came up from Richmond to help us. We plastered a huge dining room and kitchen in the same day. First joints were taped with drywall tape using durobond. Not mesh tape and not easy sand. There were problems in Richmond with joints cracking using mesh tape and just scratching finish mortar over the joints, so the paper tape and hard setting drywall compound was used. We did a nice job, but the mortar was difficult to trowel because it had a fine sand in it. It was like pushing a car with a trowel. However it is a very durable product. Completing a large area the same day is a great benefit.
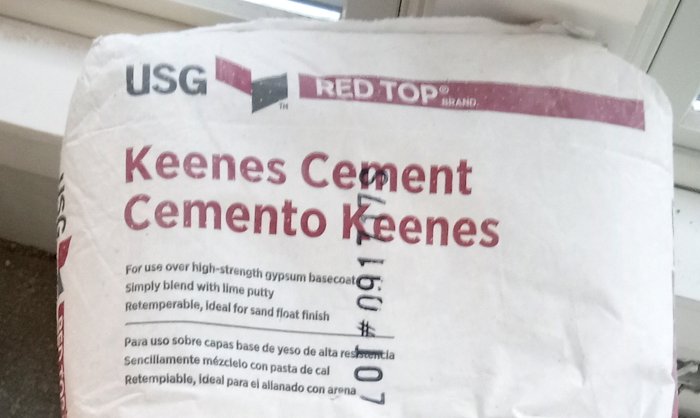
Please click here or on the picture for more about Keene's Cement.
I had to mention Keene's Cement. We use it for textures and colors. Keene's sets slow allowing large areas to be finished in one operation, avoiding joins. It would be redundant to add more about Keene's so please click here to see what I had to say. Keene's was still used widely in California when I was there. The disadvantage of Keene's cement is no one here in the Washington DC area will stock it for me, so I have to buy 63 bags at a time.
Enough for now. It feels good to finally say what I have wanted to say for years. Thanks so much dear readers, for reading all these years.